Hose failure can result in costly downtime, safety hazards, and environmental risks. Understanding the common causes and preventive measures can help ensure reliability and longevity. Below are frequently asked questions about hose failure analysis and best practices for prevention.
What Are the Most Common Causes of Hose Failure?
Abrasion and External Damage: Repeated contact with rough surfaces or sharp edges can wear down the hose exterior, leading to leaks and rupture. Use hose guards, sleeves, or reroute hoses away from abrasive surfaces.
Improper Bend Radius: Exceeding the minimum bend radius can cause kinking, leading to restricted flow and internal damage. Follow manufacturer guidelines for bend radius and use appropriate fittings.
Temperature and Environmental Conditions: Exposure to extreme heat, cold, or UV rays can degrade hose materials over time. Preventive Measure: Use heat shields, insulation, and proper storage techniques to protect hoses.
Pressure Spikes and Overloading: Frequent pressure fluctuations or exceeding pressure ratings can weaken hose integrity. Ensure pressure ratings align with application requirements and use pressure regulators where necessary.
Chemical Incompatibility: Using a hose that is not rated for the chemicals being transported can cause degradation and failure. Verify chemical compatibility using manufacturer recommendations and material safety data sheets (MSDS).
Improper Installation: Twisting, stretching, or inadequate fitting installation can lead to leaks and premature failure. Follow correct installation procedures, use strain relief supports, and avoid excessive twisting.
Lack of Maintenance and Inspection: Failure to inspect hoses regularly can lead to unnoticed wear and tear. Establish routine inspection schedules, checking for cracks, bulges, or leaks.
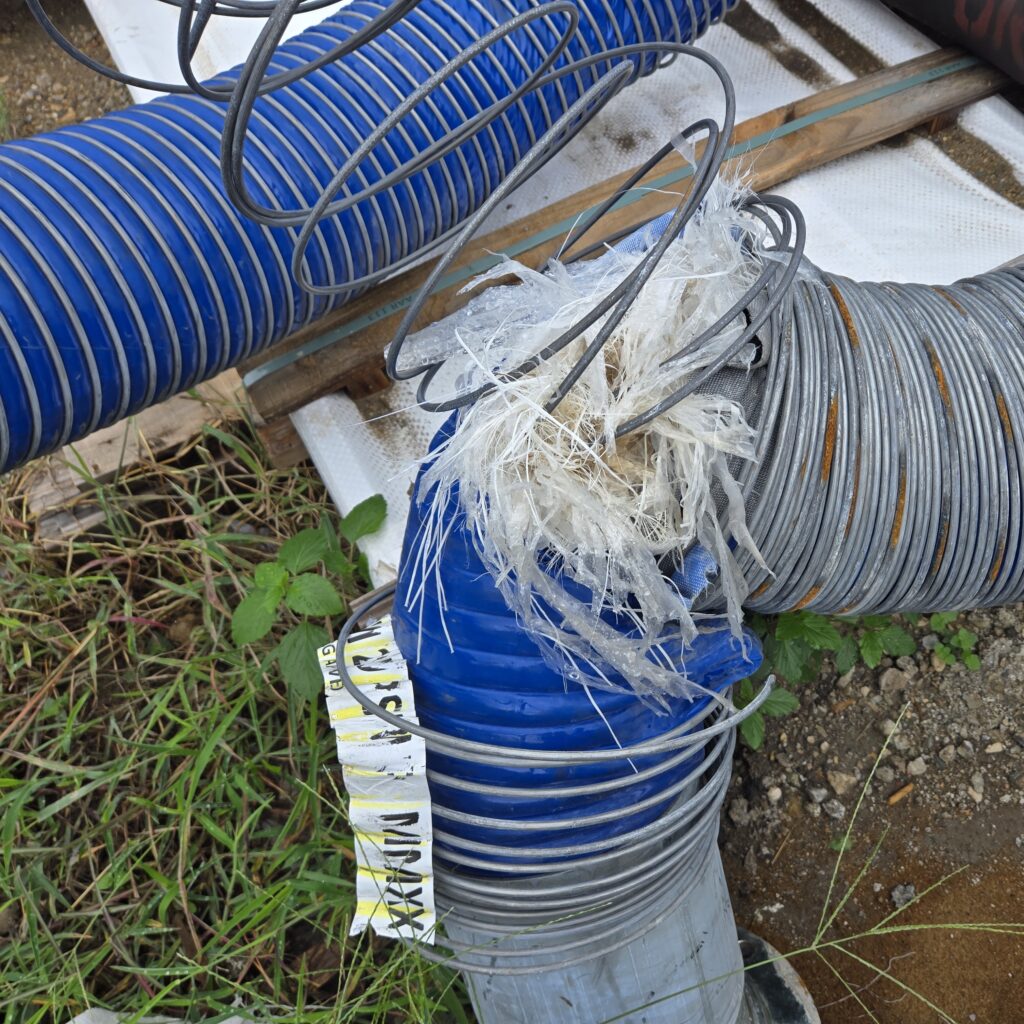
How Can You Identify and Diagnose Hose Failure?
Visual Inspection: Look for cracks, kinks, swelling, or leaks.
Pressure Testing: Conduct regular tests to detect weaknesses before failure occurs.
Operational Changes: Noticeable drops in system efficiency may indicate hose issues.
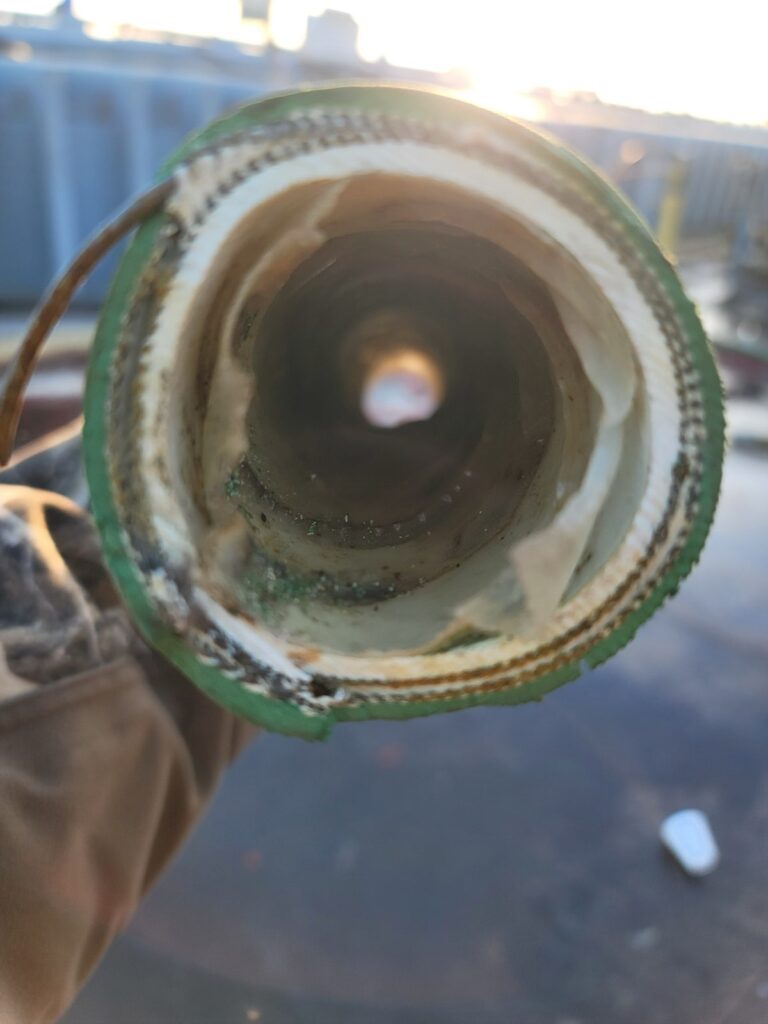
What Steps Should Be Taken After a Hose Failure?
Secure the Area: Shut down the affected system to prevent further damage or injury.
Identify the Cause: Determine if failure was due to pressure, abrasion, chemical exposure, or another factor.
Replace with Correct Specifications: Ensure the new hose meets the proper size, material, and pressure ratings.
Update Preventive Measures: Adjust inspection and maintenance procedures to avoid repeat failures.
By understanding and mitigating the causes of hose failure, businesses can improve safety, reduce downtime, and optimize operational efficiency. Contact us today for an outline of a hose failure analysis or to consult on a hose management program.